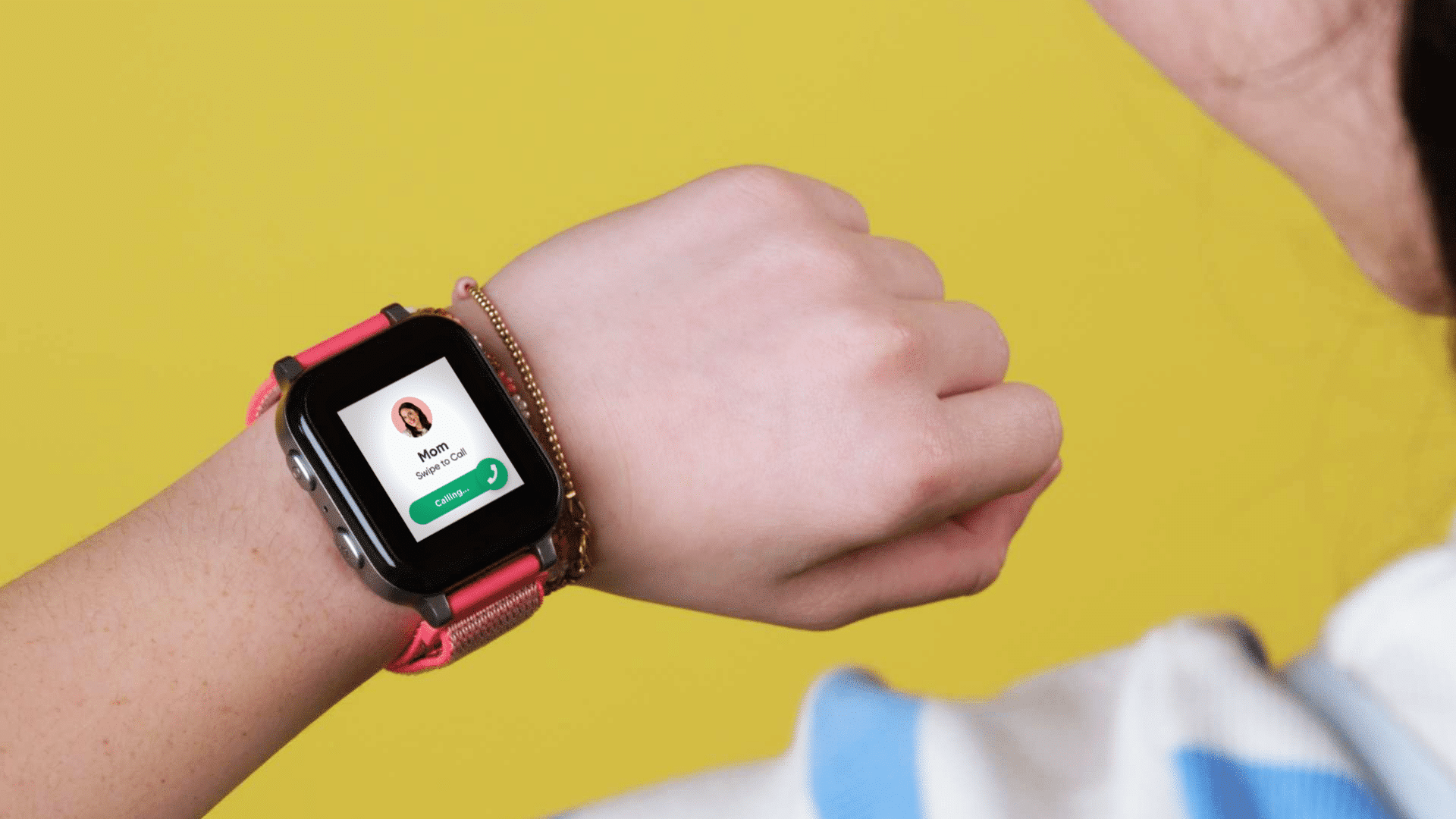
ALL RESOURCES / Case Studies
Gabb Transforms Product Reliability with Memfault - Doubling Battery Life and Delighting Parents
20-30%
Sales increased by 20–30% following improved product reliability
2.9→4.2 ⭐
Amazon rating jumped from 2.9 → 4.2 stars, boosting customer trust and visibility.
28 hours
Battery life extended to 28 hours, enhancing performance and user satisfaction.
COMPANY PROFILE
Gabb is dedicated to providing safe technology solutions for families. Their smart devices empower children with age-appropriate technology while ensuring parents maintain monitoring and control. The Gabb Watch 3e is one of their flagship products, offering GPS tracking, communication, and safety features tailored for kids.
Overview
Parents and Kids Love Gabb Watch 3e Even More After Gabb Improves Reliability and Doubles Battery Life With Memfault Insights.
Gabb uses Memfault to meet their promise to parents and is rewarded with customer reviews jumping by 2 stars and a 20%+ increase in sales for the Gabb Watch 3e.
Gabb, a leader in safe technology for kids, provides safephones and safewatches designed to making parenting easier and protect every childhood with safe tech. The reliability of these devices is critical, especially for the Gabb Watch 3e, which families count on to stay connected to their kids without exposing them to potentially harmful apps and experiences.
The Gabb Watch 3e is an Android based smart watch with cellular, WiFi and Bluetooth connectivity. Gabb’s devices are designed with great care and passion, but their engineering team struggled with a critical blind spot: Observability. Diagnosing firmware issues required months of painstaking investigation and coordination with a third-party manufacturer, creating a costly reliability gap that frustrated users and threatened market position.
The game-changer? Implementing Memfault’s observability platform. With immediate access to comprehensive field diagnostics, Gabb transformed its troubleshooting process from months to days. Gabb parents noticed, boosting Amazon reviews and significantly increasing sales.
Challenge
Lack of Visibility Created a Slow and Inefficient Debugging Process
Before adopting Memfault, Gabb faced a critical visibility gap that made identifying and diagnosing firmware issues in the Gabb Watch 3e incredibly challenging after deployment. The lack of visibility in the field, paired with a cumbersome debugging process, was frustrating.
- Limited Firmware Visibility: Gabb lacked direct insight into firmware behavior in the field and had to rely on their third-party manufacturer for analysis after organizing a device return.
- Delayed Debugging Cycles: When customers reported issues, Gabb had to get the devices back, flash debug firmware, pull logs, and then send those logs to the manufacturer.
- Lengthy Return Process: Devices had to be shipped back and forth between customers, Gabb’s HQ, and overseas manufacturers. It could take weeks or even months to get the device for analysis.
- Difficulty Reproducing Issues: Often, when returned devices were analyzed, the issues could not be reproduced, leading to dead ends and frustration. Factory resets by customers before returning devices sometimes cleared the issues, leaving no data to investigate.
One of the top priority issues for Gabb was solving a complex battery problem, which was the number one technical reason causing customers to churn. Having reliable battery performance was key to Gabb’s promise to parents and central to their mission, making resolving this issue absolutely critical.
They were frustrated because they had Datadog and other tools for visibility into software performance, but they had no visibility into the performance of the firmware. The lack of visibility into firmware performance meant issues would result in organizing returns for direct access debugging, starting a multi-month process of back and forth between Gabb and their suppliers.
Chad Baucom, Director of Product for Wearables at Gabb, described how the process was frustrating both for his team, and Gabb’s suppliers: “We would spend months sending devices back and forth between our headquarters, our manufacturers, and our battery supplier, only to hear, ‘We can’t find a problem.’ Meanwhile, more and more customers were reporting the same issue.”
The impacting reliability issues were not only causing frustration, they were getting in the way of Gabb’s mission to “protect every childhood with safe tech”. To meet this mission and ensure parents could trust Gabb devices with the safety of their children, the Gabb Watch 3e had to meet the highest standards for reliability. After a conversation with the Memfault team, Gabb knew Memfault’s Observability solution was exactly what they needed.
SOLUTION
Firmware-level Diagnostics Direct from Devices in the Field
Gabb is deeply committed to earning and keeping the trust of parents and kids. To uphold that promise, they implemented Memfault to gain the visibility needed to identify and resolve reliability issues before customers were impacted.
Once integrated, Memfault quickly transformed Gabb’s ability to resolve issues in the field. Now, instead of waiting for customer complaints and organizing device returns, the team could:
- Get automatically notified when a new issue arises and get to work right away
- Remotely diagnose and address issues before customers notice a problem.
- Root cause reliability problems without relying on lengthy manufacturer returns processes and without needing physical access to the device.
- Quickly iterate on fixes and collaborate more effectively between internal engineering and product teams and their manufacturers.
Memfault was able to quickly help Gabb solve several critical reliability issues including a battery brownout problem that had been causing devices to power off before the battery was fully depleted. “We saw that some devices were reporting rapid battery drain. With Memfault, we could collect diagnostics data directly from watches in the field and found that an overly aggressive surge limit in the firmware was shutting the watch off prematurely,” said Chad. After discovering this, Gabb worked with their manufacturer to adjust the battery surge limit, preventing unnecessary shutdowns.
“Memfault has turned an investigation process that was taking four months into a few minutes”. — Chad Baucom, Director, Product, Wearables at Gabb
Alongside resolving reliability issues, the Gabb team has used the data in Memfault to inform several other optimizations resulting in significantly improved battery performance – “Battery life went from lasting only part of the day, to 28 hours on average. That was a game changer for parents and kids.,” Chad added.
The Gabb team now uses Memfault’s battery Device Vitals data to monitor battery performance fleet-wide and track changes between firmware versions. This constant monitoring means that if any issues arise, they can identify and address them before they impact customers.
Memfault has been so transformative that Gabb engineers stated they would rather have it than have to hire another developer. Chad also noted, “Our engineers would probably have a mutiny if Memfault disappeared. It would be like going back to the Stone Age.”
RESULTS
Faster Fixes, Happier Customers, Increased Sales
“Memfault unwraps the mystery of what’s going on in your firmware. There’s so many things that go on in firmware at the device level that you just don’t have insight into. Memfault lets you dive into that, see what’s going on at the firmware level and solve problems.” – Chad Baucom, Director, Product, Wearables at Gabb
Memfault’s impact on Gabb’s operations has been transformative. Memfault has given them unprecedented visibility into the performance and behavior of their firmware in the field. Investigating issues takes minutes instead of months, and they’re able to make decisions and improvements based on real-world data from their devices.
Dramatically reduced debugging time from four months to a few minutes, allowing Gabb and their manufacturer to swiftly address issues.
Lowered customer support costs by 19%, as the team could proactively detect and resolve problems before they escalated.
Improved battery performance and better monitoring, with average battery life increasing to 28 hours, significantly enhancing the customer experience.
Amazon rating increased from 2.9 to 4.2 stars, leading to a 20-30% increase in sales.
Empowered the engineering team, enabling them to focus on building new features rather than debugging.
Better product reliability, reinforcing Gabb’s need of providing safe, dependable technology for kids and parents.
Chad summed up the impact: “With Memfault, we have seen customer support calls dropping across all of our big issues, including battery life. We’ve seen churn decrease. And our Amazon reviews have jumped up above four stars.” As a result of this improvement in customer reviews Gabb has also seen a significant increase in sales.
“I didn’t expect such a drastic increase in Gabb parent sentiment, and the amount of sales that we got because of that, the amount of kids we were able to protect because of that, I didn’t expect it to be that drastic!” – Chad Baucom, Director, Product, Wearables at Gabb
For Gabb, product reliability is much more than just sales— it’s about their mission, Chad said, “It’s a very personal mission for me that we have a high-quality product. We can’t be selling product that is having battery problems or having firmware problems and not be completely reliable. So, you guys (Memfault) are helping us to make our products completely reliable. And then we can keep working on fun new features and safe new features for kids and parents.”
“Our engineers would probably have a mutiny if Memfault disappeared. It would be like going back to the dark ages.”
Chad Baucom | Director, Product, Wearables at Gabb